

刀盤平衡機(jī)維修和保養(yǎng)注意事項(xiàng)
- 分類:公司新聞
- 作者:申岢編輯部
- 來源:上海申岢動(dòng)平衡機(jī)制造有限公司
- 發(fā)布時(shí)間:2025-06-08
- 訪問量:16
刀盤平衡機(jī)維修和保養(yǎng)注意事項(xiàng)
- 分類:公司新聞
- 作者:
- 來源:上海申岢動(dòng)平衡機(jī)制造有限公司
- 發(fā)布時(shí)間:2025-06-08
- 訪問量:16
刀盤平衡機(jī)維修和保養(yǎng)注意事項(xiàng) 一、日常維護(hù):預(yù)防性操作的黃金法則 刀盤平衡機(jī)作為精密加工設(shè)備,其穩(wěn)定運(yùn)行依賴于高頻次、低強(qiáng)度的日常維護(hù)。清潔工作需優(yōu)先執(zhí)行:使用無紡布蘸取異丙醇擦拭傳感器探頭與轉(zhuǎn)軸接觸面,清除金屬碎屑與油污;潤滑系統(tǒng)則需遵循”少而精”原則——在導(dǎo)軌滑塊涂抹二硫化鉬潤滑脂時(shí),用量控制在0.5g/點(diǎn),避免油脂堆積引發(fā)摩擦系數(shù)異常。緊固件檢查應(yīng)采用扭矩扳手逐項(xiàng)校核,重點(diǎn)關(guān)注法蘭盤連接螺栓的預(yù)緊力矩,其偏差值需控制在±5%以內(nèi)。
二、定期檢修:周期性深度保養(yǎng)策略 每累計(jì)運(yùn)行500小時(shí)需執(zhí)行三級(jí)保養(yǎng):
振動(dòng)頻譜分析:通過頻譜儀采集X/Y軸振動(dòng)數(shù)據(jù),識(shí)別1000-3000Hz頻段異常峰值,定位不平衡質(zhì)量分布 軸承狀態(tài)評(píng)估:采用紅外熱成像儀監(jiān)測(cè)深溝球軸承溫升,當(dāng)ΔT超過15℃時(shí)需拆解檢查保持架磨損度 傳感器標(biāo)定:使用標(biāo)準(zhǔn)振動(dòng)臺(tái)模擬0.5mm/s2振動(dòng)加速度,校準(zhǔn)電渦流位移傳感器的線性度誤差 三、環(huán)境控制:微氣候管理技術(shù)要點(diǎn) 設(shè)備周邊需維持溫度梯度≤±2℃/h的恒溫環(huán)境,當(dāng)車間濕度突破65%RH時(shí),應(yīng)啟動(dòng)除濕機(jī)并配合硅膠干燥劑雙重防護(hù)。防塵措施需構(gòu)建三級(jí)過濾體系:初級(jí)過濾網(wǎng)攔截>50μm顆粒,次級(jí)HEPA濾芯捕獲0.3μm微粒,最終在設(shè)備進(jìn)風(fēng)口加裝靜電吸附裝置。特別注意避免陽光直射觸摸屏區(qū)域,防止液晶層因熱脹冷縮產(chǎn)生像素偏移。
四、操作規(guī)范:人機(jī)交互的臨界控制 操作人員需掌握動(dòng)態(tài)平衡校正的黃金分割法:當(dāng)剩余不平衡量U≤1.5g·cm時(shí),應(yīng)采用加重法而非去重法調(diào)整;負(fù)載限制方面,嚴(yán)禁超載運(yùn)行——當(dāng)?shù)侗P直徑超過1.2m時(shí),最大允許轉(zhuǎn)速需降額至額定值的80%。數(shù)據(jù)記錄必須包含三要素:振動(dòng)相位角、剩余不平衡量、校正質(zhì)量位置,建議采用區(qū)塊鏈技術(shù)實(shí)現(xiàn)不可篡改的電子日志。
五、應(yīng)急處理:故障樹分析與響應(yīng)機(jī)制 遭遇異常振動(dòng)時(shí),應(yīng)立即執(zhí)行STOP-REPORT-ANALYZE流程:
緊急制動(dòng)后記錄轉(zhuǎn)速-振動(dòng)曲線 通過頻譜分析識(shí)別故障特征頻率 對(duì)比設(shè)備健康度數(shù)據(jù)庫進(jìn)行故障定位 異響診斷需區(qū)分高頻嘯叫(軸承缺油)與低頻敲擊(鍵槽松動(dòng)),建議使用聲級(jí)計(jì)進(jìn)行1/3倍頻程分析。當(dāng)主軸溫升超過80℃時(shí),需啟動(dòng)冷卻系統(tǒng)并檢查潤滑油的黏度指數(shù)變化,必要時(shí)進(jìn)行光譜分析檢測(cè)金屬磨粒濃度。 技術(shù)延伸:現(xiàn)代刀盤平衡機(jī)已集成AI預(yù)測(cè)性維護(hù)系統(tǒng),通過LSTM神經(jīng)網(wǎng)絡(luò)對(duì)振動(dòng)信號(hào)進(jìn)行時(shí)序預(yù)測(cè),可將故障預(yù)警提前至失效前72小時(shí)。建議每季度更新設(shè)備數(shù)字孿生模型,利用蒙特卡洛模擬優(yōu)化維護(hù)策略,實(shí)現(xiàn)全生命周期成本降低18%-25%。
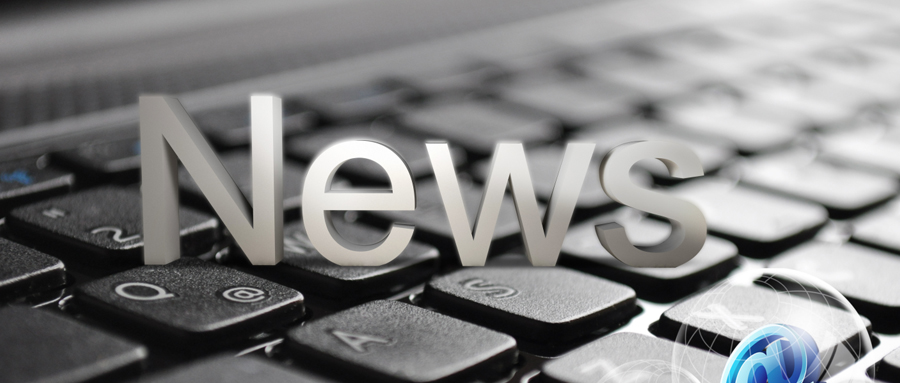