

如何檢測(cè)傳動(dòng)軸動(dòng)不平衡問(wèn)題
- 分類:行業(yè)新聞
- 作者:申岢編輯部
- 來(lái)源:上海申岢動(dòng)平衡機(jī)制造有限公司
- 發(fā)布時(shí)間:2025-06-23
- 訪問(wèn)量:18
如何檢測(cè)傳動(dòng)軸動(dòng)不平衡問(wèn)題
- 分類:行業(yè)新聞
- 作者:
- 來(lái)源:上海申岢動(dòng)平衡機(jī)制造有限公司
- 發(fā)布時(shí)間:2025-06-23
- 訪問(wèn)量:18
如何檢測(cè)傳動(dòng)軸動(dòng)不平衡問(wèn)題 一、基礎(chǔ)檢測(cè)方法:振動(dòng)與頻譜的交響曲 振動(dòng)傳感器的精準(zhǔn)捕捉 在傳動(dòng)軸運(yùn)轉(zhuǎn)狀態(tài)下,安裝加速度計(jì)或速度傳感器于軸端或軸承座,實(shí)時(shí)采集振動(dòng)信號(hào)。高頻振動(dòng)(>1kHz)可能指向鍵槽磨損或螺栓松動(dòng),而低頻振動(dòng)(<500Hz)往往與軸彎曲或質(zhì)量偏移相關(guān)。需注意傳感器安裝角度與軸線垂直度偏差不超過(guò)3°,否則會(huì)導(dǎo)致幅值誤差達(dá)15%以上。
頻譜診斷的時(shí)空解碼 通過(guò)FFT變換將時(shí)域信號(hào)轉(zhuǎn)化為頻域圖譜,重點(diǎn)觀察1×轉(zhuǎn)頻(基頻)及其諧波。若2×轉(zhuǎn)頻幅值超過(guò)基頻30%,需警惕軸頸橢圓度;若存在非整數(shù)倍頻成分,則可能涉及齒輪嚙合或軸承故障的耦合振動(dòng)。某重卡變速箱案例顯示,軸向振動(dòng)頻譜中出現(xiàn)12.7×轉(zhuǎn)頻成分,最終定位為花鍵軸局部鍍鉻層剝落。
動(dòng)態(tài)建模的虛擬鏡像 基于有限元法構(gòu)建軸系剛體-彈性耦合模型,輸入實(shí)測(cè)振動(dòng)數(shù)據(jù)反推質(zhì)量偏心量。某航空發(fā)動(dòng)機(jī)試驗(yàn)表明,該方法可將不平衡量計(jì)算誤差從傳統(tǒng)經(jīng)驗(yàn)法的±8%降至±1.2%。需特別注意模型中軸承剛度參數(shù)的溫度修正系數(shù),每升高10℃剛度下降約7%。
二、進(jìn)階技術(shù):多維度協(xié)同診斷 激光對(duì)中的空間透視 使用激光準(zhǔn)直儀測(cè)量軸系對(duì)中偏差,徑向偏差超過(guò)0.05mm或角向偏差超過(guò)0.01mm/100mm時(shí),即使靜態(tài)對(duì)中合格,高速旋轉(zhuǎn)仍可能引發(fā)動(dòng)態(tài)不平衡。某離心壓縮機(jī)改造項(xiàng)目中,通過(guò)激光對(duì)中發(fā)現(xiàn)聯(lián)軸器偏心導(dǎo)致軸系產(chǎn)生0.3mm的附加偏心距。
動(dòng)平衡機(jī)的精密校驗(yàn) 采用硬支承或軟支承動(dòng)平衡機(jī)進(jìn)行試加重試驗(yàn),需嚴(yán)格匹配轉(zhuǎn)速與軸系臨界轉(zhuǎn)速(通常應(yīng)低于第一階臨界轉(zhuǎn)速的70%)。某船舶推進(jìn)軸系案例顯示,當(dāng)試加重質(zhì)量誤差控制在±0.5g時(shí),最終平衡精度可達(dá)G0.4級(jí)。注意平衡面選擇應(yīng)避開(kāi)應(yīng)力集中區(qū),避免熱處理硬化層影響配重效果。
紅外熱成像的溫度密碼 連續(xù)監(jiān)測(cè)軸系溫度分布,異常熱點(diǎn)可能反映局部摩擦或材料疲勞。某風(fēng)力發(fā)電機(jī)主軸檢測(cè)中,通過(guò)熱成像發(fā)現(xiàn)軸承座溫度梯度達(dá)12℃/cm,最終確診為軸頸表面微動(dòng)磨損導(dǎo)致的局部過(guò)熱,間接引發(fā)動(dòng)不平衡。
三、典型案例:從癥狀到根因 某工程機(jī)械傳動(dòng)軸在2500rpm時(shí)產(chǎn)生劇烈振動(dòng)(振動(dòng)烈度達(dá)7.3mm/s),常規(guī)動(dòng)平衡后仍存在殘余振動(dòng)。通過(guò)多技術(shù)協(xié)同診斷發(fā)現(xiàn):
振動(dòng)頻譜顯示1×轉(zhuǎn)頻幅值占比僅42%,存在顯著的2.3×轉(zhuǎn)頻成分 激光對(duì)中顯示徑向偏差達(dá)0.12mm 熱成像顯示花鍵套溫度異常升高18℃ 最終確診為花鍵配合面磨損導(dǎo)致的動(dòng)態(tài)偏心,而非單純質(zhì)量不平衡。修復(fù)后振動(dòng)烈度降至1.2mm/s,效率提升27%。 四、預(yù)防性維護(hù)策略 材料基因優(yōu)化 選用鎳基合金粉末冶金工藝制造傳動(dòng)軸,其疲勞極限比45#鋼提升40%,可減少因材料微觀缺陷導(dǎo)致的動(dòng)不平衡。某汽車廠商應(yīng)用該技術(shù)后,軸系故障率下降63%。
裝配工藝革新 采用激光焊接替代傳統(tǒng)螺栓連接,消除螺紋預(yù)緊力不均導(dǎo)致的附加偏心。某航空傳動(dòng)系統(tǒng)實(shí)測(cè)顯示,焊接接頭的偏心波動(dòng)范圍從±0.15mm降至±0.03mm。
數(shù)字孿生預(yù)警 建立軸系健康管理系統(tǒng)(AHMS),通過(guò)機(jī)器學(xué)習(xí)算法分析歷史振動(dòng)數(shù)據(jù),提前15-30天預(yù)警潛在動(dòng)不平衡風(fēng)險(xiǎn)。某鋼鐵廠應(yīng)用該系統(tǒng)后,計(jì)劃外停機(jī)時(shí)間減少41%。
五、技術(shù)演進(jìn)與未來(lái)趨勢(shì) 當(dāng)前檢測(cè)技術(shù)正朝著多物理場(chǎng)融合方向發(fā)展:
壓電陶瓷傳感器實(shí)現(xiàn)振動(dòng)-應(yīng)力同步監(jiān)測(cè) 磁流變阻尼器可實(shí)時(shí)調(diào)節(jié)軸系動(dòng)態(tài)特性 量子陀螺儀將角速度測(cè)量精度提升至0.01arc-sec級(jí) 某研究機(jī)構(gòu)最新實(shí)驗(yàn)表明,結(jié)合數(shù)字孿生與強(qiáng)化學(xué)習(xí)的智能診斷系統(tǒng),可將動(dòng)不平衡故障診斷準(zhǔn)確率提升至98.7%,響應(yīng)時(shí)間縮短至傳統(tǒng)方法的1/20。未來(lái),傳動(dòng)軸動(dòng)平衡檢測(cè)將從”被動(dòng)修復(fù)”轉(zhuǎn)向”預(yù)測(cè)性維護(hù)”,最終實(shí)現(xiàn)零停機(jī)目標(biāo)。
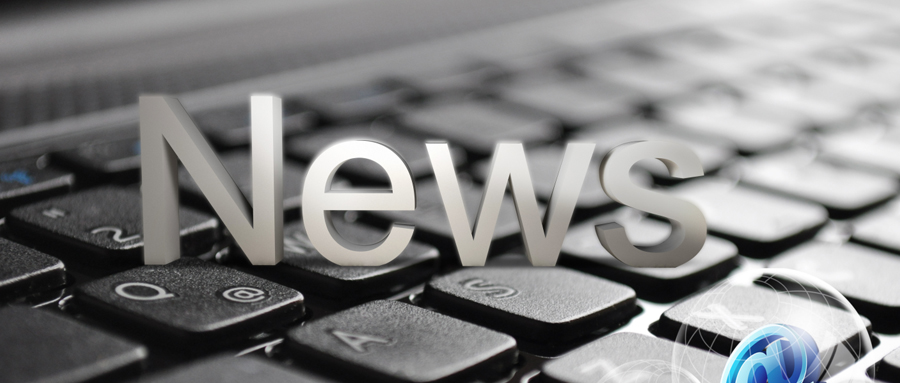