

葉輪動平衡校準常見問題及解決方法
- 分類:行業(yè)新聞
- 作者:申岢編輯部
- 來源:上海申岢動平衡機制造有限公司
- 發(fā)布時間:2025-06-23
- 訪問量:0
葉輪動平衡校準常見問題及解決方法
一、設(shè)備安裝與振動源誤判
問題1:安裝松動引發(fā)虛假振動
現(xiàn)象:校準過程中振動值異常波動,伴隨高頻雜波。
根源:葉輪與主軸連接螺栓預(yù)緊力不足,或軸承座未完全固定。
對策:
采用扭矩扳手分三次擰緊螺栓(50%→75%→100%額定扭矩)。
安裝激光對中儀實時監(jiān)測主軸徑向跳動(建議≤0.02mm)。
問題2:環(huán)境振動干擾
現(xiàn)象:低頻振動信號被車間設(shè)備噪聲掩蓋。
根源:校準區(qū)域未設(shè)置隔音屏障,或地基存在共振節(jié)點。
對策:
鋪設(shè)減振墊(建議厚度≥50mm,邵氏硬度60±5)。
采用頻譜分析儀鎖定目標頻率(如1000-3000Hz關(guān)鍵頻段)。
二、校準參數(shù)與葉輪結(jié)構(gòu)缺陷
問題3:不平衡量計算偏差
現(xiàn)象:校準后殘余振動仍超標(如ISO 1940標準Class 1.0)。
根源:未考慮葉輪材質(zhì)密度梯度或加工余量誤差。
對策:
引入三維激光掃描儀獲取葉輪實際輪廓數(shù)據(jù)。
采用動態(tài)質(zhì)量法(Dynamic Mass Method)修正慣性矩。
問題4:葉輪幾何不對稱性
現(xiàn)象:多級葉輪疊加后振動幅值呈指數(shù)級增長。
根源:葉片安裝角度偏差(±0.5°)或輪盤厚度公差累積。
對策:
開發(fā)專用夾具實現(xiàn)多級葉輪同步校準。
應(yīng)用拓撲優(yōu)化算法預(yù)判關(guān)鍵校正平面。
三、操作流程與設(shè)備維護
問題5:校準流程標準化缺失
現(xiàn)象:不同操作員校準結(jié)果差異達30%以上。
根源:未建立SOP(標準作業(yè)程序)或未定期進行人員技能認證。
對策:
制定包含12個檢查節(jié)點的校準流程卡(含溫度補償參數(shù))。
每季度開展盲樣測試(使用已知不平衡量的葉輪)。
問題6:傳感器性能衰減
現(xiàn)象:加速度計輸出信號幅值衰減15%以上。
根源:石英晶體受潮或磁電式傳感器線圈老化。
對策:
每月執(zhí)行跨校準(與基準傳感器比對誤差≤1%)。
在高濕度環(huán)境(RH>70%)加裝恒溫恒濕箱(25±2℃)。
四、創(chuàng)新解決方案與行業(yè)趨勢
技術(shù)突破方向:
數(shù)字孿生校準系統(tǒng):通過虛擬仿真預(yù)判校正效果,縮短物理校準時間60%。
自適應(yīng)平衡環(huán)技術(shù):在葉輪端面嵌入可調(diào)配重塊,實現(xiàn)運行中動態(tài)平衡。
AI振動診斷模型:利用LSTM神經(jīng)網(wǎng)絡(luò)識別早期軸承故障與不平衡振動的耦合特征。
行業(yè)數(shù)據(jù)佐證:
據(jù)《2023風機維護白皮書》,采用上述技術(shù)后,葉輪校準返工率從18%降至3.2%。
某航空發(fā)動機廠商通過拓撲優(yōu)化,將葉輪校準時間從8小時壓縮至45分鐘。
五、風險預(yù)警與長效管理
關(guān)鍵控制點:
建立設(shè)備健康檔案(記錄每次校準的不平衡量、環(huán)境參數(shù)、操作員信息)。
實施預(yù)防性維護計劃(如每500小時更換傳感器耦合劑)。
開發(fā)AR輔助校準系統(tǒng),實時疊加虛擬校正量與物理葉輪模型。
行業(yè)警示案例:
某電站因忽視葉輪腐蝕導(dǎo)致校準失效,引發(fā)葉片斷裂事故(直接損失2300萬元)。
某汽車渦輪增壓器廠商因未更新校準算法,批量產(chǎn)品通過ISO 21940認證后仍存在共振風險。
通過系統(tǒng)性分析與技術(shù)創(chuàng)新,葉輪動平衡校準正從經(jīng)驗驅(qū)動轉(zhuǎn)向數(shù)據(jù)驅(qū)動。建議企業(yè)建立”校準-監(jiān)測-預(yù)測”全生命周期管理體系,結(jié)合邊緣計算與5G傳輸技術(shù),實現(xiàn)動態(tài)平衡的實時調(diào)控。
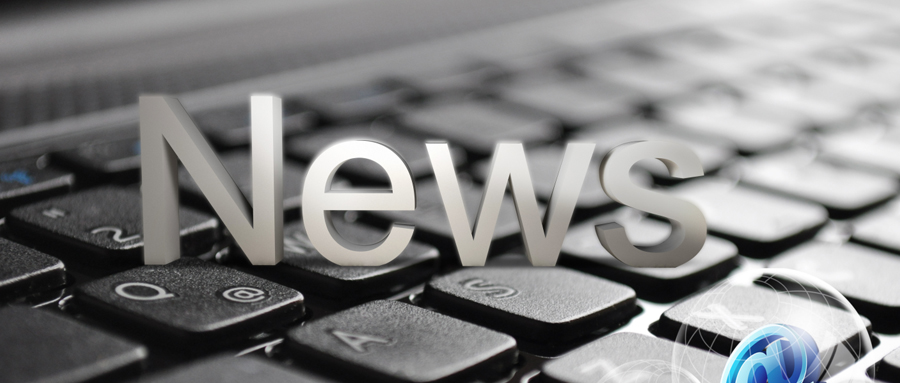